In the realm of construction, where precision and timing are everything, the sudden flameout of a self loading concrete mixer can halt operations and disrupt schedules. This unexpected event not only causes downtime but also poses a potential risk to safety on the site. Addressing this issue effectively requires a thorough understanding of the root causes, immediate corrective actions, and proactive measures to prevent recurrence.
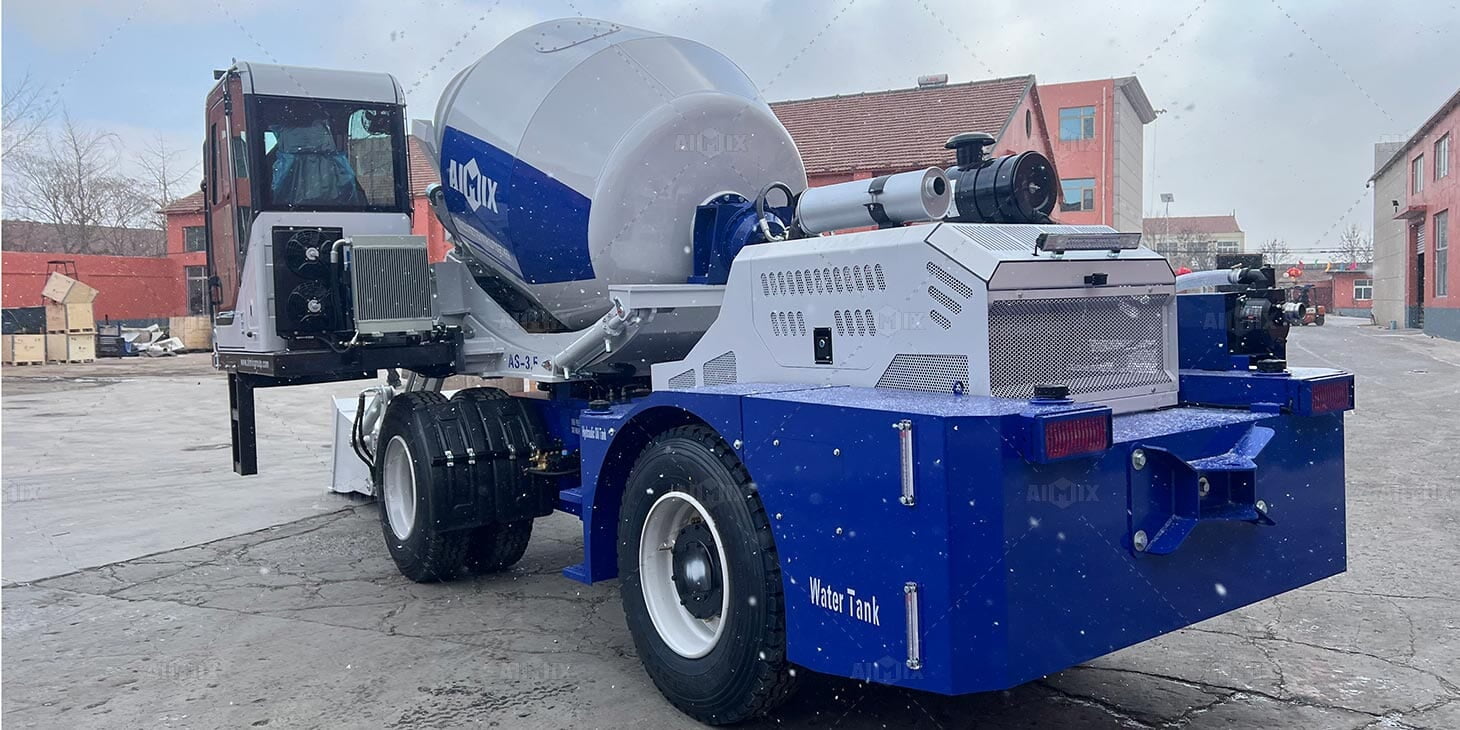
Understanding the Causes of Sudden Flameout
A sudden flameout in a self-loading mixer is rarely a random event. Identifying the underlying mechanical failures is the first step in addressing the problem. Engine malfunctions, such as issues with the fuel injection system or air intake, are common culprits. A clogged fuel filter, for instance, can restrict the flow of fuel, leading to an abrupt shutdown. Similarly, a malfunctioning sensor or an electrical fault in the ignition system can trigger a flameout, leaving the machine inoperable.
External factors also play a significant role in causing flameouts. Harsh weather conditions, such as extreme cold, can affect the performance of the engine by causing the fuel to thicken, making it difficult for the engine to run smoothly. Additionally, operating the mixer at high altitudes, where the air is thinner, can lead to an improper fuel-air mixture, resulting in engine failure. Recognizing these factors is crucial for diagnosing and resolving the issue effectively.
Immediate Actions to Take After a Flameout
When a flameout occurs, securing the worksite should be the top priority. The operator must ensure that the mixer is parked in a safe location, away from any ongoing construction activities or hazards. This minimizes the risk of accidents or injuries caused by an immobile machine on a busy site.
Once the site is secure, conducting a preliminary inspection is essential. This involves checking the basic components of the mixer, such as the fuel levels, battery connections, and the condition of the engine. If the cause of the flameout is not immediately apparent, further investigation may be required, including checking the fuel filter, air intake, and electrical system. Identifying and rectifying the issue quickly can prevent prolonged downtime and allow operations to resume with minimal disruption.
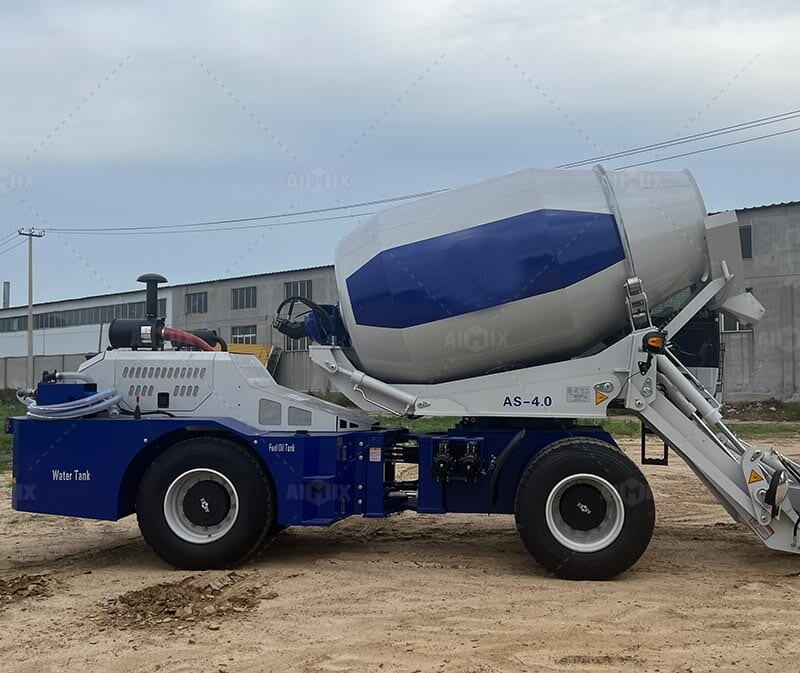
Preventive Measures for Future Operations
To avoid future flameouts, implementing regular maintenance protocols is essential. Routine checks of the engine, fuel system, and electrical components can help identify potential issues before they lead to a flameout. Replacing worn-out parts, such as fuel filters and spark plugs, and ensuring that the mixer is always fueled with clean, high-quality diesel, can significantly reduce the risk of unexpected shutdowns.
In addition to maintenance, training operators in best practices is crucial. Ensuring that they are well-versed in the correct operation of the mixer, including how to handle it in extreme weather conditions or at high altitudes, can prevent many of the issues that lead to flameouts. Regular training sessions and updates on new operational techniques can empower operators to manage the equipment more effectively, reducing the likelihood of sudden flameouts and enhancing overall productivity on the construction site.